Are you planning to retrofit your Virginia beach home with cellulose insulation? Understanding the local requirements and best practices is crucial. This guide simplifies key points about cellulose insulation retrofits in Virginia, covering insulation requirements, building codes, and considerations for existing homes.
We’ll explore how to stay compliant while improving your home’s energy efficiency. By the end, you’ll have a clear roadmap for your cellulose insulation project, ensuring proper density, heat retention, and wall protection without compromising vapor barriers.
What Are the Insulation Requirements in Virginia?
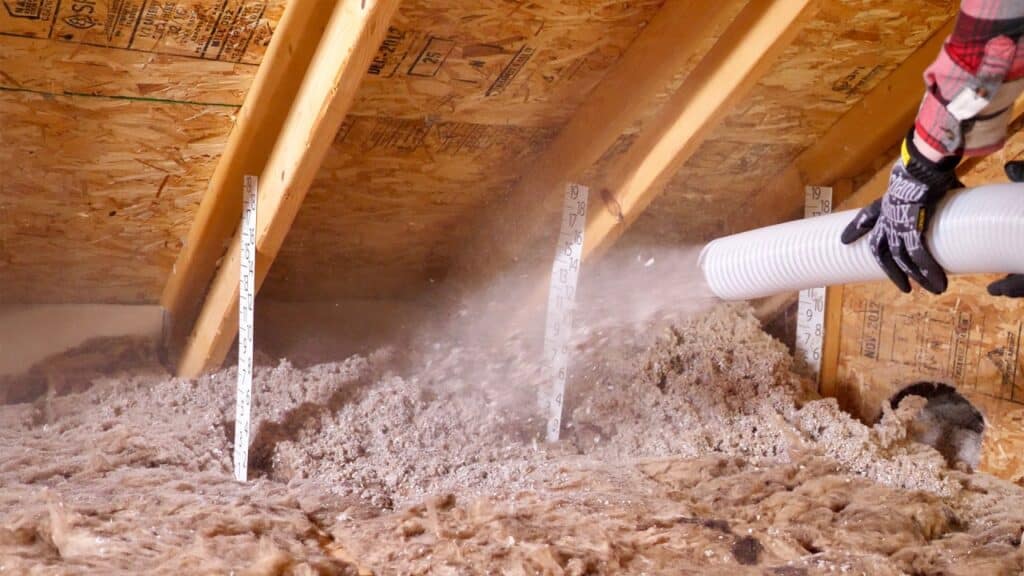
Virginia’s insulation requirements align with the 2021 International Residential Code (IRC) with amendments by the Virginia Uniform Statewide Building Code (USBC). For attic insulation in residential buildings, the state mandates different R-values depending on the climate zone and attic type, rather than a uniform R-38 requirement.
The R-value requirements for attic insulation in Virginia are as follows:
- Northern Virginia (Zone 5): R-49 for vented attics, R-60 for unvented attics
- Central Virginia (Zone 4): R-49 for vented attics, R-54 for unvented attics
- Southern Virginia (Zone 3): R-38 for vented attics, R-44 for unvented attics
When retrofitting existing homes with cellulose insulation, contractors must ensure proper coverage and depth to meet these standards. This often involves adding insulation to the attic floor or between roof rafters to achieve the required R-value.
While spray foam insulation is an option, cellulose remains a popular choice for retrofitting due to its cost-effectiveness and ease of installation. It can be blown into attics and wall cavities, providing excellent coverage and thermal performance. Cellulose insulation is eco-friendly, being made from 85% recycled newspaper, which is more than double the recycled content of any other type of insulation.
In Virginia, blown-in cellulose insulation must have markers showing thickness in inches (mm), placed at regular intervals, and visible from the attic access.
For existing homes with insulation of R-30 or higher, meeting updated code requirements may not be necessary. However, new construction and major renovations must follow current codes.
Cellulose insulation is usually 30-50% cheaper than spray foam and provides excellent soundproofing, with an STC rating of 44-68, compared to spray foam’s 39.
Building insulation requirements may vary depending on the specific location within Virginia and the type of construction. Homeowners should consult local building codes and licensed insulation contractors to ensure compliance when undertaking a retrofit project.
What Does the Building Code Require for Cellulose Insulation?
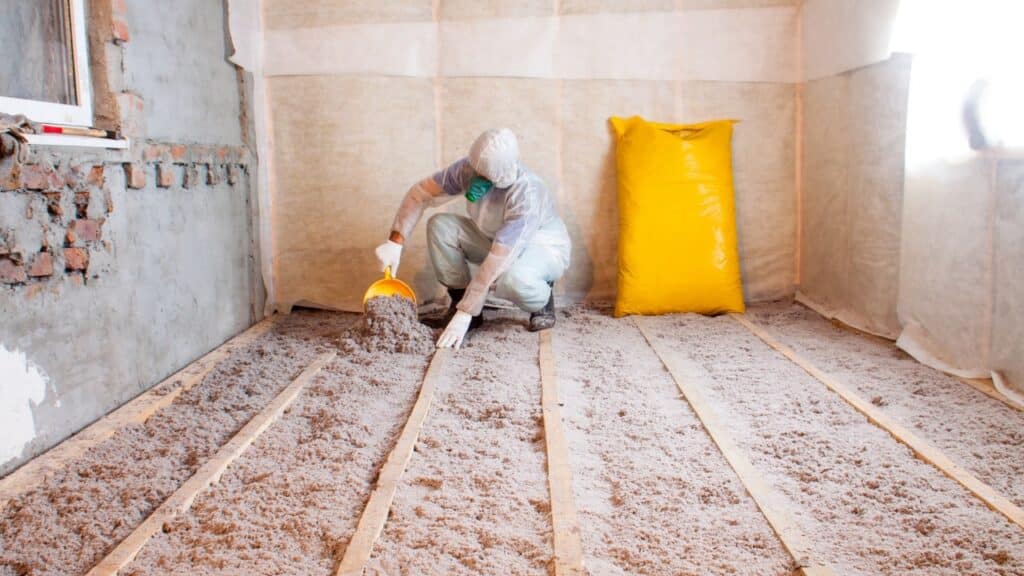
Building codes in Virginia require cellulose insulation to meet specific R-value standards for different areas of the home. In attics, a minimum R-38 is typically mandated, while crawl spaces often require R-19 or higher, depending on the climate zone.
Cellulose insulation must be properly installed to maintain its effectiveness. This includes ensuring adequate coverage between joists and avoiding compression, which can reduce its insulating properties and impact air conditioning efficiency.
The building code also addresses fire safety concerns. Cellulose insulation must be treated with fire retardants and installed with proper clearance from heat sources, such as recessed lighting fixtures or chimneys.
When retrofitting existing homes, care must be taken to avoid moisture issues. Proper vapor barriers and ventilation are essential, especially in crawl spaces and attics, to prevent drywall damage and maintain the insulation’s performance over time.
Category | Requirement |
---|---|
Installation | – Cellulose must be installed at ~3.5 pounds per cubic foot to prevent settling (for walls). |
– Thickness must be marked in inches on visible attic markers at regular intervals. | |
Fire Safety | – Cellulose must be treated with fire retardants. |
– Maintain a 3-inch clearance from electrical devices unless they are “IC-rated.” | |
Moisture Control | – Perform air sealing before insulation installation. |
– Ensure proper ventilation in attics and crawl spaces. | |
– Vapor barriers are not typically required in Virginia for attic floor insulation. | |
Additional Considerations | – Homes with R-30 or higher insulation may not need to meet updated codes. |
– Avoid covering eave vents with insulation to maintain attic ventilation. |
Do Existing Homes Have to Meet New Insulation Codes?
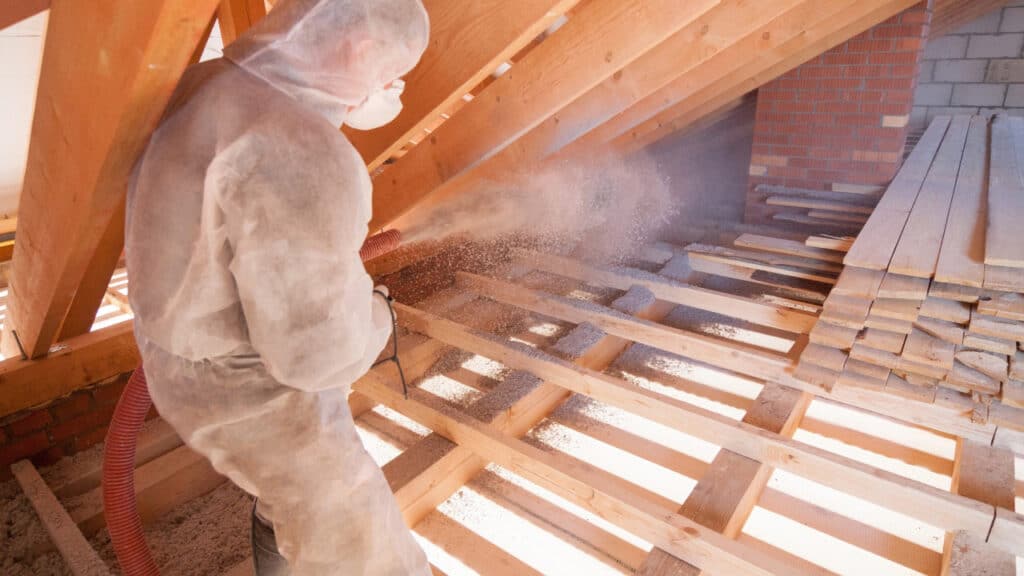
Existing homes in Virginia may not always need to meet new insulation codes, but upgrading insulation can offer significant benefits. Here’s what homeowners should know:
Do you need to upgrade?
For existing homes in Virginia, if the current insulation level is R-30 or higher, you may not be required to meet the latest code requirements. However, this doesn’t mean upgrades aren’t beneficial or recommended.
What about major renovations?
Major renovations often trigger the need for existing homes to meet new insulation codes in Virginia. When homeowners replace windows, add brick veneer, or significantly alter the building’s structure, local authorities may require upgrades to meet current energy efficiency standards. This includes ensuring proper insulation around new wood framing and addressing potential thermal bridging issues.
Cellulose insulation is particularly effective during major renovations due to its ability to fill irregular spaces and conform around obstacles like electrical boxes and pipes. When retrofitting, contractors must carefully remove any existing cardboard or fiber-based materials before installing new cellulose insulation to achieve optimal performance.
The following table outlines common renovation scenarios and their insulation implications:
Renovation Type | Insulation Consideration |
---|---|
Window Replacement | Seal gaps and add insulation around frames |
Brick Veneer Addition | Install continuous insulation behind new exterior |
Attic Conversion | Upgrade to R-38 cellulose in roof rafters |
Wall Reconfiguration | Dense-pack cellulose in new and existing cavities |
Other Items to Consider When Retrofitting
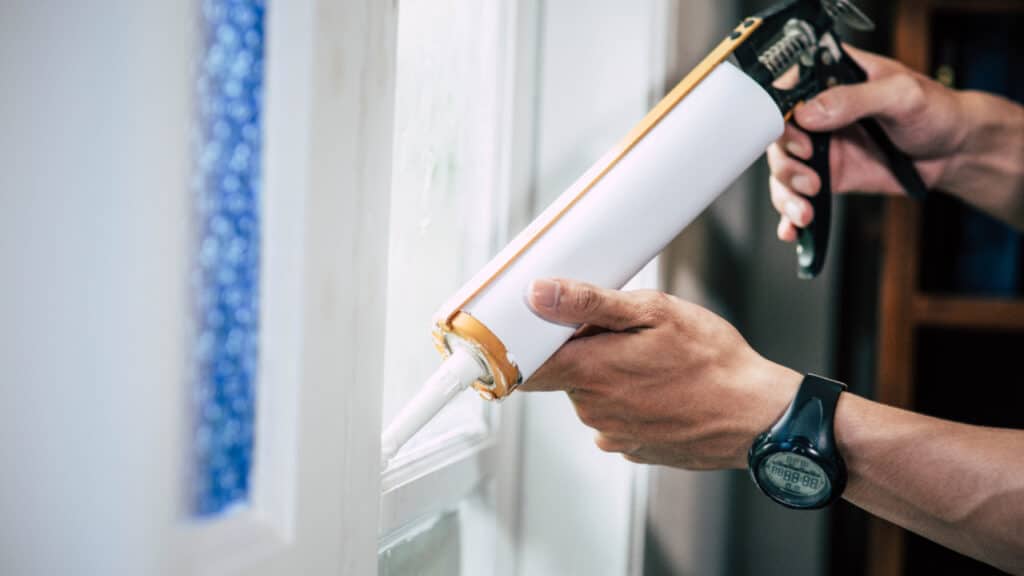
When retrofitting cellulose insulation in Virginia homes, several key factors need to be considered to ensure optimal energy efficiency, safety, and comfort. Here are the main aspects to focus on:
Air sealing
Homeowners should focus on sealing gaps in the building envelope, including areas around windows, doors, and where different building materials meet. This process helps prevent air leakage, which can compromise the insulation’s effectiveness and increase energy costs.
Special attention should be given to basements and garages, as these areas often have significant air infiltration points. Sealing these spaces not only improves energy efficiency but also reduces the risk of moisture-related issues. Proper air sealing techniques, such as using appropriate sealants and weatherstripping, ensure that the cellulose insulation can perform optimally throughout the home.
Before adding insulation, it’s essential to perform air sealing to prevent air leakage, which can compromise the insulation’s effectiveness and increase energy costs.
Ventilation
Homeowners should consider installing ventilators in attics and crawl spaces to regulate moisture levels and prevent condensation on floors and ducts. Adequate ventilation helps maintain the effectiveness of cellulose insulation by reducing the risk of mold growth and structural damage.
When retrofitting with cellulose insulation, it’s important to assess existing ventilation systems and make necessary improvements. This may include adding soffit vents, ridge vents, or gable vents to ensure proper air circulation. Proper ventilation also helps regulate indoor temperature, reducing the load on HVAC systems and improving overall energy efficiency.
When retrofitting, it’s important to create a balance between insulation and ventilation. Proper ventilation helps regulate indoor temperature, reducing the load on HVAC systems and improving overall energy efficiency.
Electrical safety
Homeowners must ensure proper clearance around electrical fixtures, especially recessed lighting, to prevent overheating and fire hazards. This includes installing insulation baffles and maintaining a minimum 3-inch clearance around fixtures, which contributes to improved indoor air quality and reduced condensation risks.
When retrofitting with cellulose insulation, homeowners should consider upgrading to energy-efficient LED lighting fixtures. This aligns with green building practices and enhances overall energy savings. Additionally, proper sealing of electrical penetrations helps prevent air leakage and moisture intrusion, which can impact insulation performance during heavy rain events.
The following table outlines key electrical safety considerations:
Electrical Component | Safety Consideration |
---|---|
Recessed Lighting | Install insulation baffles, maintain a 3-inch clearance |
Junction Boxes | Ensure accessibility, seal penetrations |
Wiring | Inspect for damage, and upgrade if necessary |
Outlets and Switches | Install foam gaskets to prevent air leakage |
Homeowners should also consider hiring a professional to assess their home’s specific needs and ensure compliance with local building codes.
How to Stay Compliant?
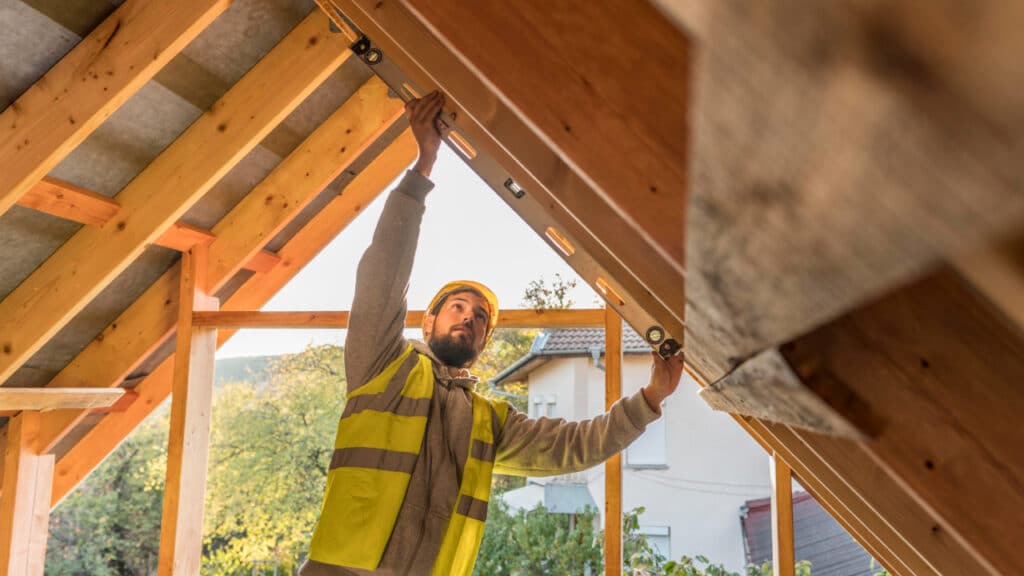
To stay compliant when retrofitting cellulose insulation in Virginia, homeowners must adhere to local building codes. These regulations often specify minimum R-values for different areas of the home, including attics, walls, and crawl spaces.
Proper installation is crucial for compliance. Homeowners should ensure that cellulose insulation is installed to create an effective air barrier, particularly around windows and other openings in the building envelope.
When retrofitting existing buildings, it’s important to consider the exterior condition. Addressing any moisture issues or structural concerns before installing cellulose insulation can prevent future compliance problems.
Regular inspections and maintenance are key to long-term compliance. Homeowners should periodically check their insulation’s condition, especially after extreme weather events, to ensure it continues to meet building standards.
Universal Insulation Doctor’s Professional Insulation Services
At Universal Insulation Doctor, we specialize in cellulose insulation retrofits that improve your home’s energy efficiency and comfort. Our expert team ensures compliance with Virginia’s building codes while providing safe, high-quality insulation solutions.
With over a decade of experience serving Chesapeake and surrounding areas, we take pride in our A+ Better Business Bureau rating, a testament to our dedication to excellence and customer satisfaction.
From enhancing attic insulation to addressing soundproofing needs, we’re here to make your home more energy-efficient and eco-friendly.
Contact Universal Insulation Doctor today at 757-962-0340 to schedule your consultation and upgrade your home with cellulose insulation!
Frequently Asked Questions
What are the current insulation requirements for homes in Virginia?
Virginia's current insulation requirements vary by climate zone, with most of the state falling under Zone 4. For new construction, attics typically require R-38 to R-60 insulation, while wood frame walls need R-13 to R-15. Basement walls and crawl spaces have specific R-value requirements as well.
How does cellulose insulation comply with Virginia's building codes?
Cellulose insulation complies with Virginia's building codes when installed to meet specific R-value requirements for different areas of the home. It must also be properly treated for fire resistance and installed according to manufacturer guidelines to ensure proper density and coverage.
Are older homes required to meet new insulation standards in Virginia?
In Virginia, older homes are not required to meet new insulation standards unless undergoing major renovations or additions. However, upgrading insulation in older homes is highly recommended to improve energy efficiency, and comfort, and reduce utility costs.
What factors should be considered when retrofitting a home with cellulose insulation?
When retrofitting a home with cellulose insulation, consider the existing insulation, air sealing needs, moisture control, fire safety, and installation methods. Assess the home's structure, ventilation, and local building codes. Evaluate cost-effectiveness and energy savings potential before proceeding with the retrofit.
How can homeowners ensure their insulation retrofit meets Virginia's compliance standards?
Homeowners in Virginia can ensure their insulation retrofit meets compliance standards by consulting with certified insulation contractors like Universal Insulation Doctor. These professionals understand local building codes, energy efficiency requirements, and proper installation techniques for various insulation types, ensuring the retrofit adheres to state regulations and maximizes energy savings.
What Are Some Common Areas We Serve?
We often work in neighborhoods like Kensington (36.876700, -76.301000) and Greenbrier (36.779100, -76.219700), providing top-quality service. Recently, we completed projects near Jeff Robertson Park and Greenbrier Country Club. Whether it’s a job in Chesapeake or Portsmouth, our team’s flexibility ensures we’re always ready to provide prompt, next-day service wherever you need us.